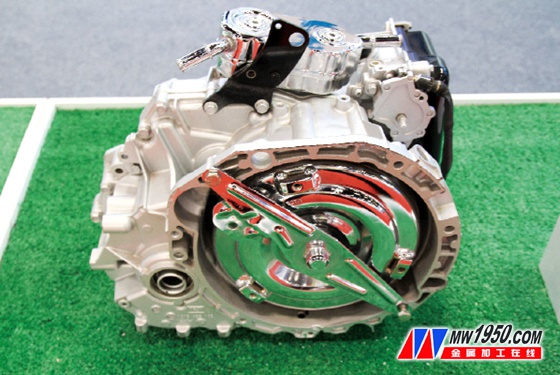
Commercial vehicle transmissions have two distinct stages in the design and performance evaluation of transmissions as the market for commercial vehicles changes. In the early days, because the commercial vehicle audience was relatively narrow, the truck drivers were basically unable to access the passenger car. The most important goal of the commercial vehicle was to be durable. The most important indicator for the commercial vehicle transmission at that time was also to assess the life indicator and strength index of the transmission. In the last ten years, because the domestic auto market has been expanding, passenger drivers and commercial vehicle drivers have mostly overlapped, resulting in the increased demand for commercial vehicle comfort. In particular, the requirements for shifting performance are increasing. How to effectively improve the shifting performance of commercial vehicle transmissions, and ensure that "light passenger car, heavy and light" is the inevitable trend of major transmission manufacturers in the current environment.
Nowadays, when it comes to transmission shifting performance, most people start to calculate the synchronizer capacity, synchronizer shifting force and so on. Improve the shifting performance of the transmission by changing the synchronizer ring from a copper ring to a steel-based molybdenum ring, from a steel-based molybdenum ring to a carbon particle ring or a carbon fiber ring (by increasing the friction coefficient of the synchronizing ring to increase the shifting capacity), or From single-cone synchronizer to double-cone synchronizer, double-cone synchronizer is changed to three-cone synchronizer (by increasing the friction surface of the synchronizer to improve shifting performance), which is completely improved around the theoretical dynamic shifting force of the synchronizer. . Although these methods have greatly improved the transmission shifting performance in theory, the actual loading verification is far from the theoretical level, because the influence of the static shifting force of the transmission and the shifting performance of the transmission peripheral system are neglected. influences.
Static shifting force
The static shifting force refers to the shifting force of the transmission when it is not working. In fact, it refers to the resistance that the gear needs to overcome when the transmission is not working. The static shifting force is one of the components of the overall dynamic shifting force of the transmission. The static shifting force is too large, and even if the performance of the synchronizer is greatly improved, the dynamic shifting performance cannot be improved year by year.
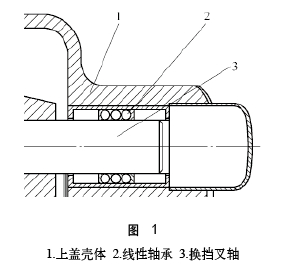
There are many factors in the static shifting force, such as the friction between the shifting shaft of the transmission and the housing, the positioning spring force of the synchronizer, the positioning spring force of the shifting shaft, the positioning force of the top cover, the gear sleeve and the tooth holder and the gear combination. Friction between the teeth and various related resistances. When designing and manufacturing the transmission, in addition to the positioning force required to ensure the shifting feel, all other relevant resistances are as small as possible from the handle of the gear. For example, the transmission shifting shaft and the housing shift shaft hole surface roughness value Ra=0.8 μm or less are required, so that the sliding friction coefficient between the shifting shaft and the housing is reduced, and the frictional resistance is minimized to the transmission shifting performance. Affected, in some high-end light trucks and passenger car transmissions, the shifting shaft is not directly connected to the shifting shaft hole, but the linear bearing (see Figure 1) connection is used to minimize shifting. Frictional resistance.
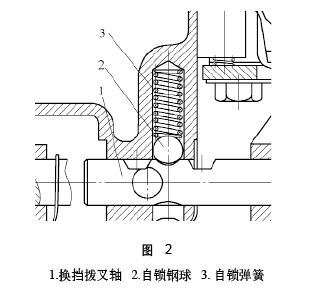
Generally, at least two spring forces must be overcome when shifting a commercial vehicle transmission: the shifting shaft self-locking force (see Figure 2) and the synchronizer push block spring force (see Figure 3). There are also some commercial vehicle transmissions that have a neutral positioning force on the top cover (see Figure 4). These spring forces are the source of the maximum force that must be overcome in addition to the frictional resistance during static shifting, while achieving the transmission change. Blocking has a clear sense of position, but when these three forces can not work at the same point of action, it will lead to very poor shifting feel, and even the entire shifting process is overcoming the spring force, resulting in no gear feeling. Nowadays, both the passenger car and the light transmission have gradually adopted the self-locking spring force and the top cover neutral positioning force to merge, and at the same time reduce the spring force of the synchronizer, so that only one force on the top cover plays a major role in shifting to ensure Gear shift comfort.
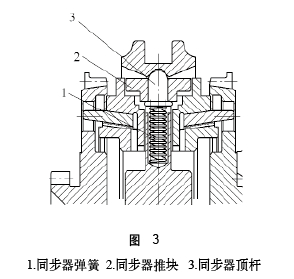
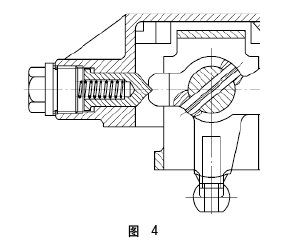
In the place where the shifting steel ball is climbed, the arc transition (see Figure 5) is adopted to avoid the sharp corner transition, ensuring a smoothness during the turning process and avoiding the stuck feeling during the shifting process. A friction reducing pad is added between the self-locking steel ball and the self-locking spring. When the gear is changed, the steel ball changes from sliding friction to rolling friction. The popular Schaeffler mechanism can also be used to ensure the smoothness of the self-locking steel ball.
Synchronizer gear holders and toothed sleeves are also generally subjected to gear shaping and broaching to ensure the smoothness of the direction of the gear when manufacturing, or to use powder metallurgy to manufacture synchronizer adapters and sleeves in light transmissions. Self-lubricating effect to reduce frictional resistance.
Shift stroke effect
Research on commercial vehicle transmissions at home and abroad, the shifting stroke of the transmission itself has gradually become a trend, which is also a very effective way to improve shift performance. As shown in Figure 6, assuming a shifting radius of 25mm, the shifting stroke is originally 13mm. When the shifting stroke is adjusted to 10mm, if the shifting stroke of the transmission is guaranteed to match the original stroke, the external shift of the transmission can be appropriately increased. The arm length and the shift lever ratio are increased, which is equivalent to the lever ratio being changed from the original 1 to 1.3, which greatly improves the shifting performance of the transmission. Therefore, in the case of ensuring the transmission shifting engagement length, the shifting stroke of the transmission should be minimized in the design.
Driven disk assembly effect
From the calculation of the shifting force and shifting time of the synchronizer, it can be known that when the transmission speed ratio is determined, that is, after the speed difference is determined, the greater the inertia that the synchronizer needs to overcome, the synchronizer shifting force and the shifting time (or Said shift shift) will increase significantly. Relative to the gears, shafts, etc. inside the transmission, the maximum moment of inertia that the synchronizer needs to overcome is actually determined by the clutch disc. The attached table shows the synchronous inertia and time data required for a six-speed transmission to be converted to each gear by different manufacturers' 380 driven discs.
Comparison of synchronous inertia and time between different manufacturers
It can be clearly seen that when the inertia of the driven disc is increased by 7%, the moment of inertia to be overcome by the shift and the shifting time required under the same shifting force are simultaneously increased by 4%.
Conclusion
The transmission cable efficiency and the rigidity of the cable bracket can directly affect the shift performance of the car. The improvement of the shifting performance of the car can not only improve the shifting performance of the transmission, but also improve the performance of the synchronizer of the transmission. It can only be improved from the whole transmission and from the transmission system to be more economical and comprehensive. The shifting performance of the car.
Refrigeration Gas
Refrigeration Gas,Refrigeration Compressor Oil,Base Oil For Refrigeration,Gas Refrigerant R134A
LONG TERM ELEC. CO., LTD , https://www.longterm-hvac.com