Designers need to understand the relationship between materials and heat treatment, and know how to select the right material for the part under tension and torque conditions.
First, material selection
The designer first selects the material and structure form from the role of the part in the product. The material selection can be considered from the following aspects.
Part function
When selecting materials, if the part is not the main force-bearing part or the force is small, you can choose ordinary carbon steel; if the part is subjected to a large load, first consider the strength of the part, then choose high-quality carbon steel. Or alloy steel to meet the required strength of the part, and medium carbon steel and alloy steel to be quenched and tempered; some parts are not stressed, but are vulnerable to fatigue load; some long-term friction, the surface of the part needs Good wear resistance, when surface treatment can be used to improve fatigue resistance and wear resistance.
2. The relationship between the performance of the part and the hardenability and tempering properties of the material
When the material has heat treatment requirements, the hardenability of the material should be considered. The hardenability of the material is firstly related to the material itself, and secondly to the thickness of the material workpiece. The material workpiece thickness parameters in the design manual are obtained from the test block test, and the test block size specifications are small, the designer should pay attention to the actual application.
(1) Effect of hardenability on mechanical properties of the material The property of obtaining the depth of the hardened layer after quenching of steel is called hardenability. After the material is quenched, the distance from the surface to the internal martensite structure at 50% is the depth of the hardened layer. Generally, the hardenability of alloy steel is higher than that of carbon steel, and the same diameter is 50mm round steel, one material is 45 steel and the other is 35CrMo steel. After quenching, 35CrMo steel is completely hardened from the surface to the core, and its mechanical properties are evenly distributed along the cross section. The tensile strength and yield strength are the same from the surface to the core. After quenching and then high temperature tempering, the obtained tissue is tempered sorbite structure from the surface to the core. The cementite is distributed in a granular shape and has high strength and toughness. For 45 steel, the hardenability is relatively poor, the core is not hardened, the structure is lamellar sorbite, the toughness is low, the tensile strength and yield strength are reduced from the surface to the core, and the toughness is from the surface to the heart. The part is enlarged and its mechanical properties are unevenly distributed along the section.
(2) Factors affecting hardenability The factors affecting hardenability are critical cooling rate v k , which is the minimum cooling rate of all martensite structure. The smaller the value, the easier it is to obtain martensite structure. The hardenability of steel is strong. With the increase of carbon content, the hypoeutectoid steel will reduce the critical cooling rate, the isothermal transformation curve will shift to the right, and the hardenability will increase. The hypereutectoid steel will exceed 1.2%~1.3% with the carbon content (mass fraction). When the critical cooling rate will increase, the isothermal transformation curve will shift to the left, and the hardenability will be significantly reduced. The alloying elements Mn, Mo, Cr, Al, Si, Ni, etc. can reduce the critical cooling rate of steel and make the hardenability of steel A big increase. If the designed parts are required to be completely hardened, the alloy steel containing the above alloying elements will be beneficial to improve the hardenability of the material, and the required properties of the parts can be achieved after quenching + tempering.
(3) The performance after tempering at different temperatures is to exert the best performance of the material, and some medium carbon steel or alloy steel must be subjected to quenching and tempering treatment. Depending on the purpose of the material used, the tempering temperature can be controlled to obtain different tissues. The tempering temperature is 150-250 ° C, and the obtained structure is tempered martensite with a hardness of 58-64 HRC. This tempering is mainly to reduce the residual stress and brittleness of the material. Some tooling requires high hardness and high wear resistance, and often uses low temperature tempering to obtain the desired material properties. The tempering temperature is 350 to 500 ° C, and the obtained structure is tempered tortonia with a hardness of 35 to 45 HRC. Medium temperature tempering is mainly used for the treatment of various springs, so that it has high elasticity and yield strength while maintaining a certain toughness. The tempering temperature is 500-650 ° C, and the obtained structure is tempered sorbite with a hardness of 200. ~350HBW. If the designed parts require quenching and tempering treatment, it is appropriate to pay attention to the W C of the material between 0.27% and 0.5% when selecting materials. The carbon content is too low to be hardened, and the required strength cannot be achieved after tempering; If the amount is too high, the toughness is insufficient and the overall mechanical properties are deteriorated.
Second, the problems in the design of parts under tension or torsion load
For example, the test boring bar of our well-free workover rig (see Figure 1) is a trapezoidal threaded connection with a specification of Tr120×10 and a tensile force of 1600KN, which is subject to a large load. After calculation, the thread has to withstand a tensile force of 160t, and the safety factor of the thread is 3. After calculation, the yield strength of the material is ≥800MPa, and the use of the material is safe. Since the entire section is subjected to force, and the mechanical properties of the surface and the core of the part are required to be uniform, a steel that can be completely hardened is selected. Compared with alloy steel, high-quality carbon steel is superior to high-quality carbon steel in hardenability. 35CrMo steel pipe is used with a wall thickness of 45mm. The material has a hardenability value of 42 J/(11 to 32), and J is a terminal hardenability. After quenching, the hardness is 42 HRC at a distance of 11 to 32 mm, and the critical diameter of the oil quenching is 31 to 90 mm.
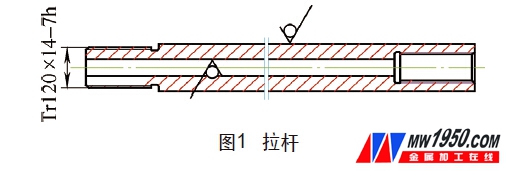
According to the hardenability curve of 35CrMo steel, it can be seen that (32~46) J/22.5 is obtained in the middle part of the pipe wall thickness, which means that the steel pipe is completely hardened and fully meets the design requirements. After quenching and tempering treatment, the hardness is 290-320HBW, the tensile strength reaches 990MPa, and the yield ratio of alloy steel is about 0.85. It can be seen that the yield strength can reach 840MPa. And the entire section is basically hardened, the tensile strength and yield strength of the surface are basically the same as the core, so that the material can withstand the tensile strength to achieve the best performance. The hardened microstructure is a tempered sorbite structure from the surface to the core, wherein the cementite is distributed in a granular shape and has high toughness. If the center of the material is not hardened, the surface structure is tempered sorbite and the core structure is lamellar sorbite. First of all, the tensile strength and the yield strength of the core are significantly reduced, and the required yield strength is not achieved. When the stress generated by the external load of the tie rod is greater than the yield strength of the material, it is broken. Second, both impact toughness and fatigue performance are reduced, resulting in a decrease in overall performance. According to the different hardness required on the surface of the material, different tempering temperatures can be selected to control the hardness of the surface. The test rod is clamped by the slip. If it is too hard, the slip will be damaged, and the too soft slip will slip. Can not hold the tie rod, can not be used, the hardness of the tie rod is more suitable between 290 ~ 320HBW, so the tempering temperature after quenching is controlled at 400 ~ 440 °C to meet the hardness and strength requirements.
Another test torsion bar in our factory (see Figure 2) is mainly used to transmit torque with a maximum torque of 24kN·m. According to the function, only profiles with a circular cross section, such as round tubes and round bars, can be selected. The weight of the round pipe is lighter than that of the round steel, which is convenient for lifting, which can save materials and reduce design cost. Therefore, it is more suitable to select a round pipe. When the torsion bar is subjected to the torsion force, the outer diameter of the round pipe is subjected to the maximum shearing force, and the shearing force of the inner tube is gradually reduced, and the core portion is not subjected to the shearing force, so that the thickness of the material is required to be half-hardened, according to the shearing. The cutting strength and the torque to be withstand are selected from 45 steel pipes with a wall thickness of 20 mm. The hardenability value of the material is 43J/(1.5-3.5), the critical diameter of water quenching is 5-20mm, the yield strength after quenching and tempering is over 305MPa, and the maximum shear force of the outermost circle of the steel tube after calculation is 90.5MPa. After calculation, the safety factor is 2, which is completely full of design requirements. The surface hardness is 290-320HBW, which meets the design requirements. The hardness is close to the hardness of the tubing and is suitable for the clamping of the kava tooth. It is not necessary to select a material with high hardenability.
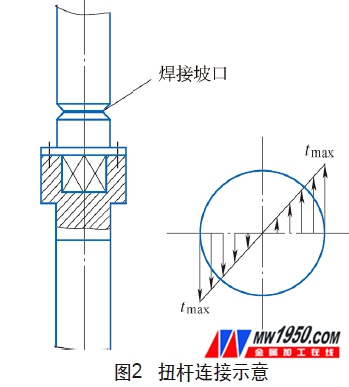
Third, fatigue damage and wear resistance problems
In addition to selecting suitable materials, it is helpful to know some heat treatment methods and strengthening processes to improve the fatigue strength and surface wear resistance of materials.
Surface hardening treatment
The pulleys produced by our factory are many. The pulley groove is often subject to friction by the wire rope and is easy to wear, and the load is also constantly changing. Therefore, the surface of the pulley groove must have certain wear resistance and fatigue resistance. High-frequency induction hardening on the surface of the pulley groove improves wear resistance and fatigue resistance.
High-frequency quenching can raise the surface of the workpiece to 800-1000 ° C in a few seconds, while the core temperature is still close to room temperature, and the surface has exceeded the phase transition temperature (727 ° C). At this time, the surface of the workpiece undergoes a phase transformation to form an austenite structure, which becomes a cryptocrystalline martensite structure after quenching and cooling. Since the martensite is larger than the austenite, the surface metal expands and is pinched by the inner layer metal to generate residual compressive stress, which can improve the fatigue strength and improve the fatigue resistance of the part. When designing the pulley, ZG270-500 with higher strength, better plasticity and toughness, with a WC of 0.4%, is a medium carbon steel (suitable for surface quenching between 0.4% and 0.5%). If the carbon content is too high, the brittleness of the hardened layer will be increased, the plasticity and toughness of the core will be lowered, and cracking will occur when quenching. On the contrary, the hardness and wear resistance after quenching will not meet the design requirements. The hardness of the surface of the pulley groove after quenching is 40 to 50 HRC, and the depth of the hardened layer is 1.5 to 2.5 mm. Note that if the material's comprehensive mechanical properties are poor, the material should be quenched and tempered before surface hardening, which can be determined according to the purpose of the part.
2. Surface strengthening
The gear used on the rig product bears heavy load, and the tooth and the tooth are easy to wear. The tooth surface needs higher hardness to improve the wear resistance, while other parts need better toughness and plasticity. Therefore, the carburized steel is selected. More appropriate. For example, 20CrMnTi and WC are between 0.10% and 0.25%, belonging to low carbon steel, and the core has good toughness and plasticity. Surface-enhanced carburizing treatment is used to improve the wear resistance of the tooth surface. The surface WC of the workpiece after carburizing is suitable for 0.85%-1.05%. Carburizing is generally carried out by gas carburizing at a temperature of 900 to 950 °C.
After carburizing, low temperature tempering treatment is carried out, and fine flaky martensite and a small amount of cementite structure are obtained on the surface, and the hardness is 56-62HRC. The core structure varies with the hardenability of the steel, such as low carbon steel, the core structure is ferrite and pearlite, the hardness is 10-15HRC, and the low carbon alloy steel 20CrMNTi is high in hardenability. The heart is composed of tempered low-carbon martensite and ferrite. Its hardness is 35-45HRC. It has high strength and good toughness and plasticity, but its carburizing and quenching temperature is high and the parts are deformed greatly. Finally, the finishing process should be carried out, generally using grinding, paying attention to the depth of carburizing to leave the grinding allowance.
Another surface strengthening process is nitriding, the nitriding temperature is 500-570 ° C, and a very high hardness nitride is formed on the surface of the part after nitriding. Because of the large residual compressive stress in the nitriding layer, the tensile stress generated under the fatigue load can be offset, the fatigue failure process is delayed, and the nitriding layer is dense and continuous, which effectively improves the corrosion resistance of the part. Since the nitriding temperature is below A1 (727 ° C), the required hardness can be achieved without quenching after nitriding, so the nitriding deformation is small. There are 4 brackets in the slip assembly on the workover rig of our factory (see Figure 3). The inside of the bracket has a high-precision arc surface and a circular arc groove, and the outer side is a slope. The slope is stressed and easy. Wear causes the part to fail. Therefore, the 42CrMo alloy steel with better hardenability is selected, and the roughing is followed by quenching and tempering treatment. The raw materials are forged, which guarantees the quality of the blank. In order to ensure the concentricity of the arcs of the four brackets, only the whole machining of the circular arc surface and the circular arc groove is used, and then cut into 4 pieces, and then processed elsewhere. If carburizing and quenching treatment is used, the deformation is large, which affects the dimensional accuracy of the processing, which leads to scrapping of the parts. At this time, nitriding treatment is more suitable, and the 42CrMo material contains alloying elements such as Cr and Mo which are easily nitrided. After nitriding treatment, the deformation of the part is small, and the dimensional tolerance of the circular arc surface and the circular arc groove is not affected. After the nitriding, the bevel surface is finely ground or ground to achieve the performance requirement. Since the nitriding layer is relatively thin and the thickness is 0.24 to 0.5 mm, attention should be paid to the finishing allowance.
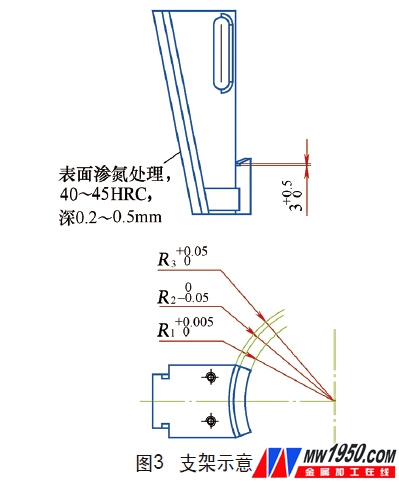
It can be seen that the designer has some knowledge of heat treatment, which can guide the rational selection of materials, help to improve the design quality, reduce the manufacturing cost, improve the production efficiency and performance, and prolong the service life of the product.
About the author: Wen Haipeng, Material Processing Institute of the Fourth Machinery Plant of Sinopec Petroleum Engineering Machinery Co., Ltd.
Jiangmen Duramp Electric Co., Ltd , https://www.durampled.com