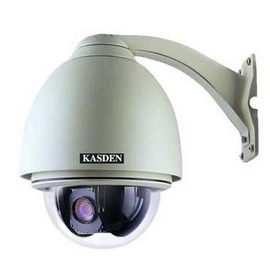
The surveillance lens refers to the camera lens of the surveillance camera. Since the surveillance camera is only a single video capture device, the pixel and resolution of the lens are higher than the video head of the computer, but cannot catch up with a professional digital camera or DV.
In practical applications, users often ask questions about how far the camera can see the object or how wide the scene can be seen by the camera. This is actually determined by the focal length of the selected lens. The resolution of the selected camera is related to the resolution of the monitor.
The focal length of the optical system refers to the distance from the main point of the light group to the focal point. The focal length of the lens is actually the focal length of the combined light group that constitutes the lens. It determines the size of the captured image. When the object at the same position is shot with different focal length lenses, the size of the scene taken by the camera with a long focal length lens is Large, on the contrary, the size of the scene taken by the camera with a short focal length lens is small.
In theory, any kind of lens can take very distant objects and make a small image on the imaging target surface of the camera, but limited by the pixels, when the image is small enough to be smaller than one pixel of the image sensor. Hours, it is no longer possible to form an image of the subject, even if the image is a few pixels in size, the image is difficult to distinguish what.
However, the lens construction and installation techniques are not unfathomable. However, during the construction process, due to various reasons, the lens installation and installation errors are not uncommon, and the lens structure or circuit is damaged. So, what are these common problems?
Lens adapter ring assembly sequence error Lens adapter ring assembly sequence is the largest blind spot in the lens installation of the engineer, and the direct consequence of this is the lens damage. Because the C and CS adapter rings are used in lens mounting, many engineers often lock the adapter ring first with the camera and then lock the lens into the adapter ring. Some of the lenses will be designed. With a sliding structure that matches the back focus of the camera or the mechanical back focus adjustment of the release screw on the camera, these adjustments require that the lens be rotated on the mating ring or driven with the mating ring to achieve the best focal length Clear point. However, due to the sequencing error when the engineer assembled, the adapter ring is deadlocked on the side of the lens. As a result, in the absence of automatic back focus (ABF) function, loosening the mating ring not only fails to adjust the back focus, but also causes the lens threads to wear out due to improper force or the screw thread on the plastic material on the lens is twisted. Broken.
Lens assembly without gloves causing damage to the coating In the lens assembly process, the most common construction failure for the engineer is the absence of gloves or protection resulting in damage to the coating. Due to the lack of protective lens (installed with lens protection cover for installation) and the awareness of careful protection and careful handling of precision equipment or optical components during construction, some engineers often find their fingerprints on the lens surface when the lens is assembled. Or other dirt. Experienced engineers will take appropriate chlorine dioxide and wiping cloth or buckskin to wipe, but there are still some people who, for the sake of simplicity, choose to use a touch of clothes or wipe with improper paper towels, not only coating the surface of the lens lens. Destructive, but also hurt the video screen and the lens "negative."
When the lens is mounted in the protective cover and the distance between the windows is not properly set. When installing the electric lens, it is most likely to be neglected that the lens is not installed in the protective cover and the window distance is not properly left. When engineers do depth of field or focal length adjustment after construction, they sometimes find that the picture actually sees the image reflected by the camera or the lens itself on the protective cover. At this time, even if the depth of field (ZOOM) or focus adjustment (FOCUS) is still not changed, the screen rotation cannot be changed. Inexperienced engineers mistakenly believe that the camera itself has not been adjusted properly, but it is due to the fact that the lens is installed in the protective cover with the wrong spacing.
The lens is assembled without proper protection During the assembly of the lens, most engineers will carefully assemble the lens. The price of the lens is not cheap, and the lens is damaged due to slight carelessness. However, some engineers neglect the protection when assembling cameras and lenses, and even choose to perform on site. In the absence of protective cushions and other preventive measures, it is extremely easy to cause damage to the lens surface, damage to the internal aperture shutter sheet, or sand adhesion to the lens.
Lens Assembly Automatic Iris Connection Circuit Welding Error With the efforts of the lens manufacturers, most types of lenses have already implemented pre-wired and connector processing. In this way, the lens servo motor burned due to similar circuit welding errors no longer exists. However, due to the presence of certain electric lenses on the supply or on-site protective cover, engineering personnel still need to understand and be familiar with these wiring and fine-circuit welding techniques. The author once discovered that the accident of welding and short-circuiting of the auto iris drive circuit joints of all lenses occurred in a project, which caused great losses and cost consumption to the engineering works. As an engineering company, it was necessary to prevent such problems from happening.
An electric Butterfly Valve is a type of valve that uses an electric motor to control the opening and closing of the valve. The valve consists of a disc that rotates around a central axis to control the flow of fluid or gas. When the electric motor is activated, it rotates the disc to open or close the valve. Electric butterfly valves are commonly used in industrial applications such as water treatment, chemical processing, and HVAC systems. They are preferred over manual valves because they offer precise control and can be operated remotely.
Electric Butterfly Valve,Electric Actuated Butterfly Valve,Electric Butterfly Valve Price,Electric Butterfly Valve
WUXI KVC-VALVE , https://www.wxkaiweixi.com