As part of the US Chocolate Mountain Geothermal Resource Assessment project, Sandia and the US Navy Geothermal Project Office (USN GPO) hosted a demonstration trial.
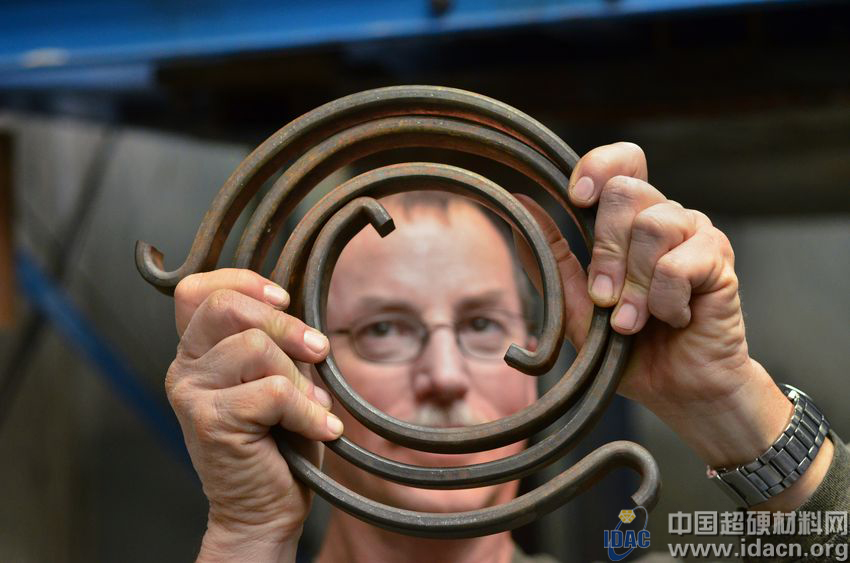
The staff used a torsion spring to simulate the rotational vibration of the drill bit while it was working.
Researcher David Raymond said that because oil and gas exploration and development is less difficult than geothermal drilling, PDC bits were originally used to drill oil and gas. The drilling geological environment of oil and gas resources is usually a rock formation with loose texture and complete structure. This geological structure generally does not require liquid circulation technology to remove rock debris, and does not need to consider the problem of cooling and cooling of the drill bit.
However, with the deeper drilling and development of oil and gas resources, drilling will inevitably encounter similar problems in the geothermal drilling process: the deeper the drilling formation, the harder the rock, the more rock debris, and the lower the underground temperature. The higher it is.
Raymond explained that the geothermal resources are often composed of igneous rocks and metamorphic rocks, which are much harder than sedimentary rocks in oil and gas resources. Moreover, igneous rocks and metamorphic rocks are rich in quartz, and abrasives such as quartz often have a large impact on the wear of the drill bit and the vibration of the drill bit. These rocks, which are in a broken form, change the impact load of the drill bit and cause great damage to the drill bit.
At this stage, geothermal drilling is still a technical challenge that needs to be improved in terms of cost. Raymond added that the drill must drill hard rock and withstand high temperatures and pressures. The US Department of Energy's future plan is to achieve a deep depth of 30,000 feet through the improvement of drill technology to obtain more geothermal resources.
In terms of economic risks, the prospects for geothermal drilling are also not optimistic. A large number of oil and gas fields have been developed every year in the United States, and abundant minefield development resources can provide a lot of room for development and improvement of oil and gas drilling bits. However, the development of geothermal drilling industry has been faltering. There are few geothermal well fields developed each year. The research and development costs of supporting facilities and corresponding drill bits are high and the technology is difficult. Every development of a geothermal well field means that there is a risk that it will not be able to recover the cost.
Sandia's project is carried out at the Bilima Camp Mine, which is made up of granite and andesite, both of which are commonly encountered in geothermal drilling. A key element of the project is the testing and evaluation of PDC bits and the corresponding technology in a real drilling environment.
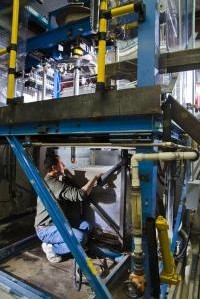
Workers are checking the original PDC bit on the drilling equipment
In the field test, two PDC bits drilled 1,291 feet in a 3,000-foot deep field, drilling 30 feet per hour, and drilling depth was three times that of the control cone bit in the control group; the two drills were only four days long. It was worn out.
In the next phase of the research project, Sandia will continue to work with NOV to study the performance of the drill bit and further improve the design and construction of the drill bit. The project was sponsored by the US Recovery and Reinvestment Act and was supervised by the EGS Drilling Systems Technology Development and Field Experiments team. (Compiled from "Polycrystalline diamond drill bits open up options for geothermal energy"; Translation: Wang Xian)
Lathe parts processing refers to the manufacturing process of creating custom metal parts on a lathe machine. Lathe machine is a versatile tool used in various industries including automotive, aerospace, and electronics. Lathe parts processing involves using a lathe machine to cut, shape, and form metal parts according to the required specifications.
The process of lathe parts processing involves several steps. First, the metal material is selected based on the specific requirements of the part to be produced. Once the material is chosen, it is loaded onto the lathe machine, and the cutting process begins. The lathe machine is programmed to move the material towards the cutting tool, which removes material to create the desired shape and dimensions.
Lathe parts processing can produce a wide range of parts in varying shapes and sizes. Lathe machines use a variety of cutting tools, including drills, taps, and reamers, to produce parts according to the required specifications. Additionally, the lathe can produce components with varying levels of complexity, from simple cylindrical shapes to more complex shapes with intricate details.
One of the significant advantages of lathe parts processing is its ability to produce large quantities of parts with high accuracy and consistency. Lathe machines can be programmed to produce the same part repeatedly, ensuring consistency and quality control. This is especially beneficial in industries where a large volume of identical parts is required.
Another advantage of lathe parts processing is its versatility. Lathe machines can be used to produce parts from a variety of materials, including metals, plastics, and composites. Additionally, lathe machines can produce parts with various finishes, such as polished or textured surfaces.
In conclusion, lathe parts processing is an essential manufacturing process in various industries. It offers the ability to produce customized parts with high accuracy and consistency, which is vital in industries where quality and precision are critical. With the ability to produce parts in large quantities, lathe parts processing offers a powerful solution for a wide range of applications.
Turning Operation On Lathe Machine,Grooving Operation On Lathe Machine,Reaming Operation On Lathe Machine,Drilling Operation In Lathe Machine
Lizhi Precision Manufacturing Technology Co.,Ltd , https://www.autoindust.com