NUS N04400 is a Ni-Cu-Fe-Mn Ni-based nickel-copper alloy, commonly known as Monel. The alloy has high plastic toughness and excellent anti-adhesion properties, and can be used in as-cast and heat-treated conditions.
Application overview and special requirements: mainly used in aviation fuel installations and other precision friction parts that require stable operation. For example, it is used to make the rack sleeve in the aero engine fuel pump regulator, instead of the original 30Cr13 material. In the 1980s, the extruded bar was successfully developed. Due to the difficulty in the production process and the low yield, the cast rod was developed and approved in the early 1990s.
Smelting is generally carried out by vacuum medium frequency induction furnace melting, cast iron die casting; non-vacuum medium frequency induction furnace melting can also be used, and the furnace lining is covered with acid or alkaline and glass. There are many components in the alloy, and the melting point is high. It is difficult to smelt and cast. The casting temperature is 1450 to 1480 °C.
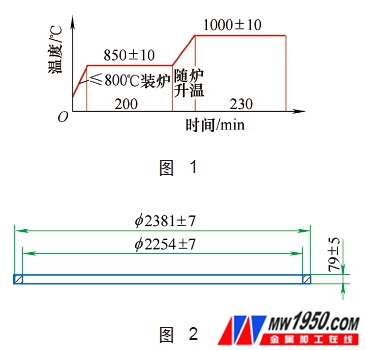
The first contact with the material, in order to ensure the first pass rate of the performance index of the forging after heat treatment, to avoid repeated heat treatment, the series of heat treatment process test of the material test bar, to determine the reasonable heat treatment process parameters, to provide reference for the heat treatment of forgings.
1. Technical requirements
The chemical composition requirements of UNS N04400 are shown in Table 1. The mechanical properties at room temperature are shown in Table 2.
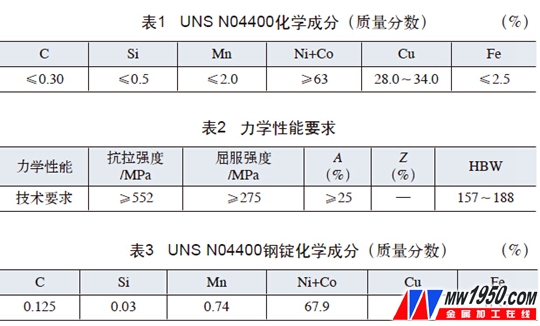
2. Preparation and test methods of test materials
(1) Forging and forging properties: The alloy is not plastic and the hot working temperature range is narrow. The chemical composition of steel ingots is shown in Table 3. The blank is rounded before forging, and the forging heating curve is shown in Fig. 1. The dimensions of the blank for boring, drawing, punching, reaping, flat end, pre-rolling and final rolling are shown in Figure 2. Final forging temperature ≥ 850 ° C, air cooling after forging.
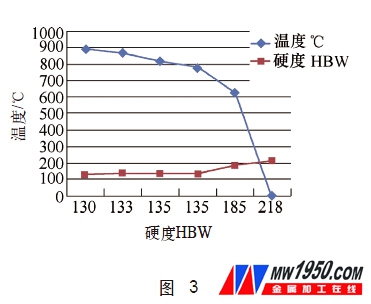
(2) Test method The heat treatment test bar was forged into a 57 mm × 57 mm × 230 mm physical and chemical test bar using a forged core. After the heat treatment, the test bar was processed into a tensile force sample having a nominal diameter of f5 mm, and the tensile force at room temperature was measured on a universal testing machine in accordance with the requirements of ASTMB564-11.
(3) Heat treatment scheme As seen from the analysis of the molten steel ingot composition, the material belongs to the Monel series alloy. Compared with the chemical composition of NCu30-4-2-1 nickel-copper alloy in China, the difference is as follows: 1 The silicon content is low. 2NCu30-4-2-1 nickel-copper alloy is a dispersion-hardening type high wear-resistant Ni-based alloy, usually called silicon-containing monel. The addition of silicon increases the strength, hardness and recrystallization temperature of the alloy, improves the casting properties of the alloy, but also significantly reduces the ductility of the alloy. The standard heat treatment process of NCu30-4-2-1 nickel copper alloy is: solid solution + aging. The chemical composition of the two grades is shown in Table 4. The strengthening of metal materials usually has heat treatment solid solution strengthening or solid solution + age strengthening, heat treatment quenching strengthening and work hardening. China's NCu30-4-2-1 belongs to the solid solution + ageing strengthening, and its chemical composition is very close to that of UNSN04400 material. Therefore, it is first considered to use solid solution + aging for strengthening. According to the above analysis, the following three test schemes were initially formulated for the material test bars, and the heat treatment was carried out using a box type electric furnace:
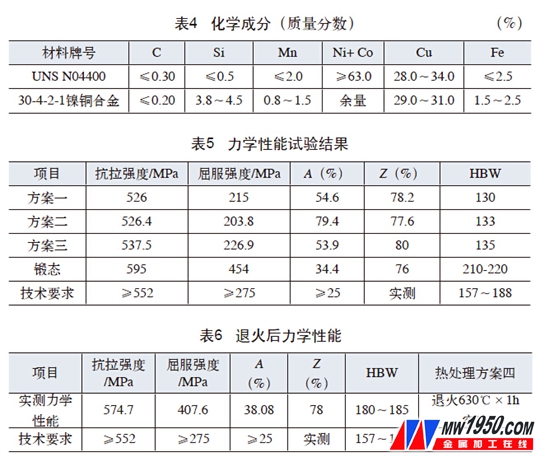
Scheme 1: Solid solution 900 ° C × 1 h water cooling + aging 580 ° C × 8 h air cooling;
Scheme 2: solid solution 870 ° C × 1 h air cooling;
Scheme 3: solid solution 815 ° C × 1 h air cooling.
3. Test results and analysis
The hardness of each sample was tested and the hardness was measured using a Brinell hardness tester. It can be seen from the hardness test results that the forged specimen has the highest hardness of 210-220 HBW, and the hardness of the same piece is the lowest, about 130 HBW. The law of hardness detection is that the hardness decreases with the increase of the heating temperature of the heat treatment, as shown in FIG. The test results are shown in Table 5. It can be seen from Table 5 and Figure 3 that the tensile strength, yield strength and hardness of the material according to Schemes 1 to 3 are decreasing compared with the forging state. As the heat treatment temperature increases, the strength and hardness decrease, and the plastic toughness increases, which is inversely proportional to the heat treatment heating temperature. Water cooling in Option 1 does not increase strength and hardness.
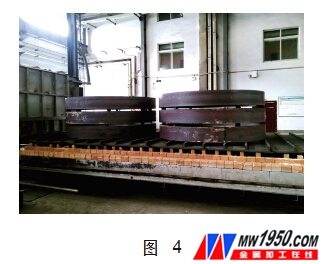
None of the above solutions can meet the technical requirements of mechanical properties, mainly because the tensile strength and yield strength do not meet the technical requirements. Although the mechanical properties of the forged state can meet the technical requirements, the hardness of the forged state is 210-220 HBW, which is higher than the technical requirement hardness (157-188 HBW). It can be seen from the analysis of the mechanical properties of the forged state that it is only necessary to reduce the hardness on this basis to meet the technical requirements. Therefore, considering the annealing treatment scheme, annealing can refine the grains, reduce the hardness, and improve the plasticity. Refer to the annealing temperature of Monel. The annealing process and the mechanical properties after annealing are shown in Table 6, which meets the technical requirements.
Therefore, the material cannot be strengthened by solid solution or solid solution + aging to meet the technical requirements, and it is necessary to refine the grains by work hardening and annealing to reduce the hardness and improve the plasticity to meet the technical requirements. Figure 4 shows the forged piece after heat treatment.
The forgings are annealed at 630 ° C × 1 h air cooling, and the mechanical properties of the forgings meet the technical requirements as shown in Table 7.
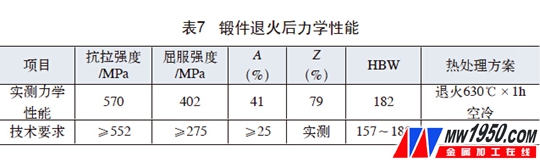
4. Conclusion
The material needs to be forged and annealed to achieve the technical properties required by the technique, and cannot be heat treated by solid solution strengthening. After forging, it is annealed at 630 ° C × 1 h air cooling to reduce hardness, eliminate stress, restore grain and improve plasticity and toughness, and the mechanical properties meet the technical requirements. The forgings are annealed and the mechanical properties meet the technical requirements.
About the author: Fan Weiwei, Guizhou Hangyu Technology Development Co., Ltd.
Carbide Boring bar is a kind of boring tool, the most commonly used occasions are hole processing, reaming, profiling, threading, etc. Boring tools can be divided into roughing boring tools and fining boring tools.
The boring tool is made of solid carbide material,and some boring tools have internal cooling holes, to flush out the chips in the holes.
Internal Profiling Boring Bar,Boring Bar Holder Lathe,Boring Bar Grooving Tool,Boring Bar For Lathe
ROYI CNC TOOL TAIXING CITY CO.,LTD , https://www.royitools.com