[China Aluminum Industry Network] 1. Construction process flow chart
2. Industrial production of aluminum profiles for glass curtain walls (1) Production and processing of industrial aluminum profiles.
a. Preparation for processing (1) Select the processing workshop and warehouse location, and arrange the processing equipment and equipment according to the production and processing flow.
(2) Carefully review the construction drawings and retest the buildings, and adjust the size of the aluminum blanks according to the actual size.
(3) Correct the processing equipment and tools to ensure the accuracy of the processing, and check regularly.
(4) Inspection of industrial aluminum profiles entering the factory must be inspected, factory certificate, certificate of origin, type, quantity, and mechanical performance report.
(5) It is necessary to check whether the oxide film on the surface of the aluminum profile is intact and free from damage. Excluding the deep-nicked and large-area-scratched raw materials, the aluminum material with distortion and bending deformation should be calibrated before cutting.
b. Machining accuracy requirements (1) Cutting material size allowable deviation Allowable deviation right angle cutting length L1.0mm
Head angle ª10'
Angle cut length length L1.0mm
Head angle ª15'
(2) There should not be obvious processing distortion at the end of cutting (3) Permissible deviation of hole position ±0.5mm, permissible deviation of hole spacing ±0.5mm, cumulative deviation not exceeding ±1.0mm.
(4) Through holes for rivets shall comply with the provisions of GB1521.
(5) Counterbore for countersunk head screws shall comply with the provisions of GB1522.
(6) Counterbores for cylindrical heads and bolts comply with the requirements of GB1523.
c. Other requirements for fabrication The aluminum profile assembly should be firm, and the connection gaps must be reliably sealed. The self-tapping screws that connect the seams should not protrude beyond the frame slots to prevent the glass from breaking when the glass is pressed locally.
(2) Glass industrial aluminum processing glass is one of the main materials of aluminum alloy glass curtain wall, which directly restricts the performance of the curtain wall, and is also the main embodiment of the curtain wall art style. Glass is a representative brittle failure material, and almost all glass is broken due to surface stress caused by tensile stress. Therefore, the manufacturer should provide the actual allowable load value of the glass based on the test data. Tempered glass has a high internal stress, so once the part is damaged, the whole piece will be crushed. Therefore, special care must be taken in handling and storage. And once the surface is scratched, the stress concentration develops and breaks naturally after a period of time. Prevent scratching of glass during processing and construction installation. Tempered glass may have a spontaneous explosion rate of about 3% during transportation and storage.
The quality requirements of tempered glass shall be implemented according to relevant national and industry standards.
The principle of performance of coated glass is mainly the principle of thin-film optics. Its main features are that it can only transmit visible light and a small part of infrared light and ultraviolet light, and can achieve energy-saving effects, and can also obtain multiple reflective colors. Coated glass technical requirements, light energy performance, size tolerances according to national and industry standards.
After the glass is cut, it should undergo edge repair and there should be no obvious defects. Glass openings, edge cuts, edge treatments are processed according to their technical specifications.
(3) Production of glass curtain wall components a. After assembly of aluminum profiles for aluminum frames, assembly shall be performed on the workbench. The assembly table surface should be flat. The assembled aluminum frame should be checked for the following items:
(1) The difference between the lengths of the sides of the aluminum frame;
(2) The difference in diagonal length of the aluminum frame;
(3) Assembly gaps between aluminum materials;
(4) The flatness between adjacent aluminum materials;
Component assembly size tolerance (mm)
Project component side length allowable deviation slot height and slot width <20002.0> 20002.5
Component to edge size difference <2000<2.0>2000<2.0
Component diagonal length difference <2000<3.0>2000<3.5
Adjacent member assembly clearance and allowable deviation of the same plane height (mm)
Project tolerance Deviation for assembly <1
Difference in the same plane height < 1
(5) Components must cooperate with each other on lines, textures, and colors;
(6) The combined components must prevent the following disadvantages: change of curvature, unevenness, and ripples;
(4) Production of hidden frame curtain wall a. Cleanliness and cleanliness of the substrate at the glue joint is the key process to ensure the adhesion of the hidden frame plate, and it is also one of the main technical measures for the safety and reliability of the hidden frame curtain wall. It must follow the following Procedure operation:
(1) Use the following cleaner non-oily contaminants: isopropyl alcohol 50%, water 50% mixed solvent oily contaminants: Dimethyl stupid (2) When cleaning, the cleaner must be poured on the cleaning cloth, not the cloth Into the container, should be cleaned in one direction, and then wipe off the volatile solvent with a second dry cloth. The second piece of cloth should be replaced immediately after it is dirty.
(3) After cleaning, glue must be injected within 30 minutes, otherwise a second cleaning is required.
(4) After cleaning the plane, do not touch it with your hands to prevent the second contamination.
b. Adhesion of double-sided tape glass must be fixed on the aluminum frame according to the design position. In the plane, the aluminum frame and glass must be accurately positioned by the reference line. Positioning fixtures are generally used to determine the exact position and the deviation is within ±1 mm.
After the aluminum frame is installed, fix it with a jig, and then affix the double-sided adhesive strip. Double-sided adhesive strips ensure the thickness and width of the seams. The thickness of the double-sided adhesive tape should be 1 mm larger than the thickness of the adhesive, because after putting the glass, the tape should be compressed by 10%. When sticking the double-sided tape, the tape should be kept straight, and press down firmly to make the tape close to the aluminum frame, but do not touch the adhesive surface. Do not peel off the release paper of the strip before placing the glass to prevent the surface from being contaminated.
Glass placed on the strip should be a successful positioning, not to move the glass back and forth, otherwise do not glue on the glass, it will be difficult to ensure that the injection structure of the adhesive bond firmly. If the sticker does not touch the cleaned glass surface, it should be cleaned again.
The double-sided adhesive tape saves environmental conditions: the temperature does not exceed 21°C and the humidity does not exceed 50%.
c. Hidden frame glass curtain wall structure glue injection construction process Structure of the hidden glass curtain wall structure bonding site, must use neutral silicone structural adhesive, caulking must use neutral silicone weathering adhesive, is strictly prohibited using acidic silicone rubber, poly Sulfur sealants and other articles, glass structural adhesives and weatherproof adhesives must be compatible with the materials they are in contact with, otherwise they cannot be used. Materials used in engineering, such as glass, laminates, pads, bats, etc., must be compatible with the adhesive. Sex and adhesion test, after the test is qualified, the order can only be used. Before the plastic injection, the validity period of the glue must be checked. The expired rubber is strictly prohibited. The structural adhesive must be glued horizontally in order to drain the air in the gap. The glue should be carefully operated. The coating should be uniform and no bubbles should be formed to ensure that the glue tank is filled with rubber and the rubber material is filled with the glue slot and raised. Before the glue gun can be removed, press the glue to flatten and compact it with a pressure plate. 5-15 minutes after the glue is used to shape the plastic seam. During this period, the scraper is used to repair the glue to make it smooth and continuous. Clean. If leaks and voids are found and bubbles are present, glue should be promptly filled. The extra silicone glue at the plastic mouth must be wiped before solidification. The inspection must be performed at the same time as the glue injection. The glass components after the glue injection should be labelled, and the “original record of the quality inspection of the glass structure assembly glue injection†should be filled in timely. , plastic models, operators, etc. to prepare for later investigation, injection finished product must be moved to the curing zone in a horizontal state.
b. Curing period management After the plastic injection, the sheet should be left to stand for maintenance, and it can be transported after being left standing for seven days. Therefore, a sufficient area of ​​standing space should be prepared.
Restoration site maintenance requirements: temperature is °C ~ 28 °C, relative humidity of 65% ~ 75%, otherwise it will affect the structure of the plastic curing effect.
Resting can be done with shelves or stacked on the ground. When mass-produced, stacking is more. When stacked, 4 to 7 blocks are generally placed, and four equal-edge cube blocks must be placed between each block. The pad can be made of foamed plastic or other elastic material, and its size deviation should not be greater than 0.5mm, so as to avoid uneven glass and crushed.
To determine the degree of cure, the cut test sample left over from the adhesive can be used. If the surface of the cut colloid glitters, it is very smooth, indicating that it has not yet cured. On the other hand, if the cut surface is flat and the color is dark, it is completely cured and can be handled.
Incompletely cured panels cannot be handled to avoid a decrease in adhesion. After being fully cured, the plates can be shipped to the on-site room for a period of 14 to 21 days so that the bond strength can be installed and installed.
After reaching 21 days strength, the peeling test can be used to test its adhesion. During the test, pull one end of the glue sample, cut 50mm in the middle of the strip with a knife, and then use the knife to pull the strip of the incision backwards. If it tears along the glue, it is acceptable. If it is peeled off on the surface of the substrate, The damage of the colloids indicates that the adhesive force is insufficient and the plates failed.
LED point light source is a new kind of energy conservation and environmental protection decorative light, using LED cold light source, the built-in microcomputer chip, can be arbitrary programming control, multiple synchronous change, monochromatic changes can also be realized synchronous colorful gradient, jump, scanning, running water light color change effect and multiple LED point light source form a lattice screen.All kinds of pictures, text and animation effects can be changed. It is a supplement of linear light source and flood lighting, which can meet the design requirements of the point line surface.
Product size
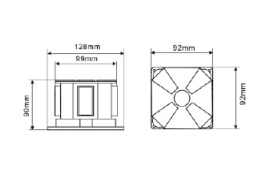
Led Point Lamp,Blue Point Led Lamp,Led Point Ovale,Led Blue Point
Jiangsu chengxu Electric Group Co., Ltd , https://www.chengxulightings.com